To the people at Indian Designs HQ, Mr. Gunashekar is the familiar figure stoically manning the sampling department. Ensuring that the indents coming in through the product developers and the merchandisers are complete, the styles to be developed have been downloaded to the tailors, and are being completed on time to be checked by the quality checkers (QCs) so that various departments can meet the buyer deadlines
But once the office hours are done Guna master returns to his home and likes to spend his evenings sitting back and watching cartoons with his daughter. And though his daughter prefers Shinchan, Doraemon is his personal favourite. (“Master” is how supervisors of tailoring departments are referred to colloquially.)
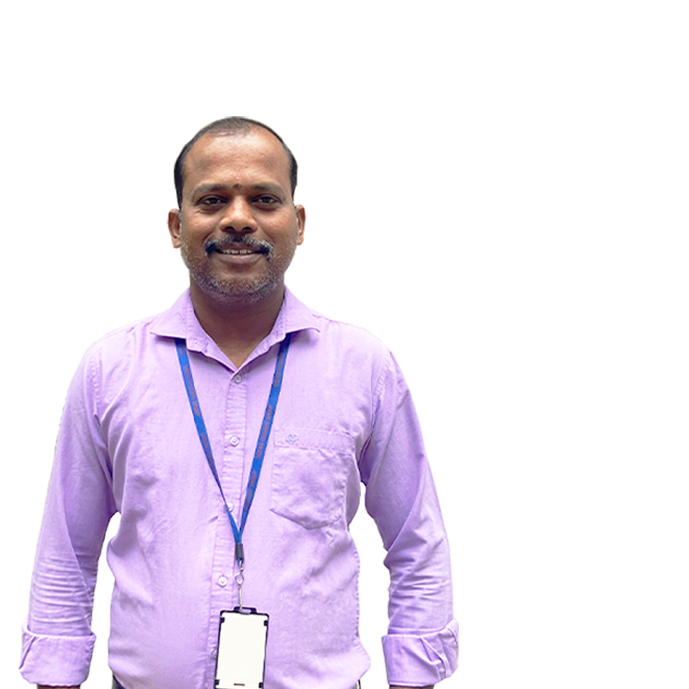
Guna master is the go-to person when a particularly complex buyer request comes in, or when a design needs to be tweaked to make production more efficient. But even veterans start from somewhere. To find out about his journey we conducted an interview with him and found out that he actually got his start at Indian Designs itself!
Guna master first started by training as a tailor in the production line. Within one year he had gained all the fundamental skills and decided to pursue some personal projects with this newfound knowledge. He even ran his own business for a few years.
Then on 27th February 2009, he returned to our company to manage the production line for one of our client brands and has been with us ever since.
Shortly after he rejoined the company he was transferred to the sampling department and was assigned its supervision. After which he has steadily progressed to managing it completely along with the department manager.
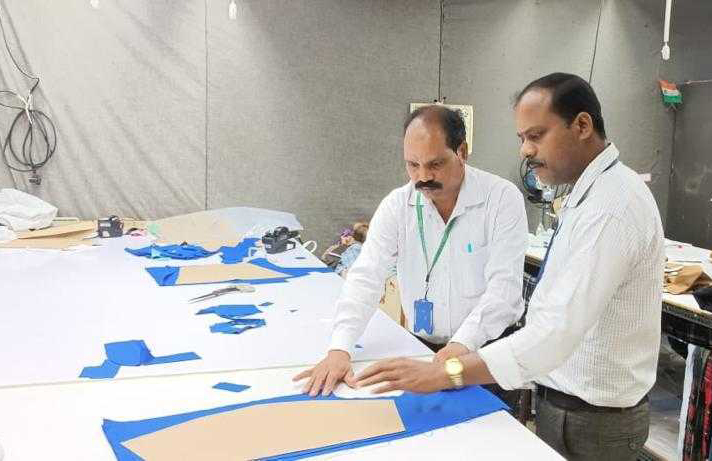
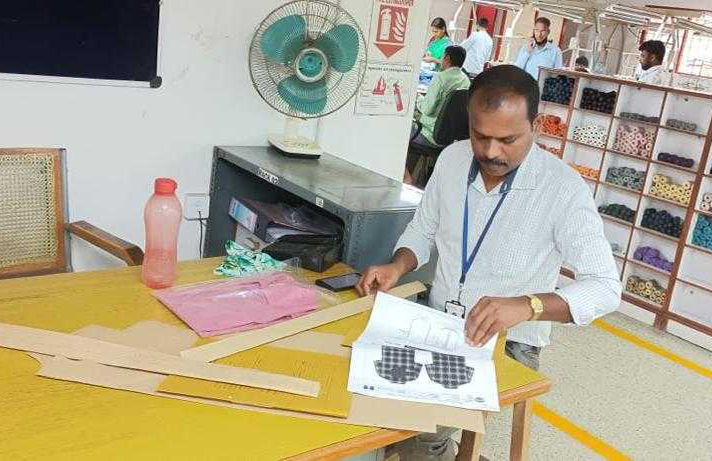
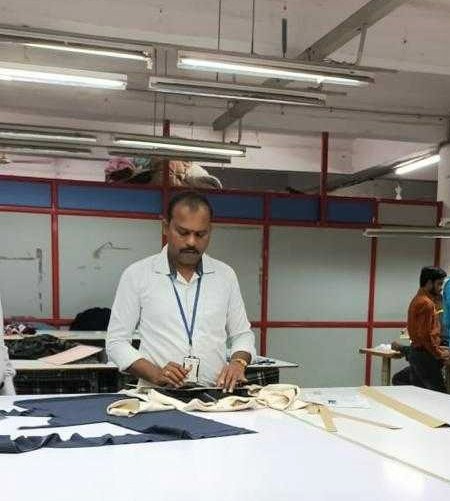
Q. Can you summarise your progress so far from supervisor to executive.
“When I first became a supervisor the number of sampling requests coming in was not a lot. Now the stakes are also much higher due to the high demand. We are trying our best to keep up with the new buyer requests that come in. But now I have the experience to handle it at this scale. Earlier too I had the knowledge required about what needed to be done for which style. But it took me some time to be able to manage things at this level. Initially, I might have required a sample garment for reference now I can guide my team to develop any garment with just the tech pack.
It took me 2 to 3 years to get to this level. For the initial years, Shekar Sir (AGM- Sampling) was there to guide me and I gradually started to step up to the lead role by myself. My role became much larger once the CAD department came in and it required Shekar Sir’s time and attention. He gave me the trust and freedom to preside over the sampling department as I seem fit as well, so, I felt a responsibility to live up to that, ensure everything was handled.”
Guna Master taking on the role of supervisor also coincided with his daughter being born. It was a time of change not just professionally but personally. His daughter is roughly the same age as the years he has been at ID.
Spending time with his daughter is a huge part of how Guna Master switches off from work.
“With the number of samples we complete in a day and the pace at which we get them done, there is no time to log them into a system and then work off the list. The list has to be maintained and tracked in the mind.”
“It’s really important for me to be able to switch off and free up my mind completely after work. And spending time with my daughter and watching cartoons with her helps me do that. Then I can come back to work recharged.”
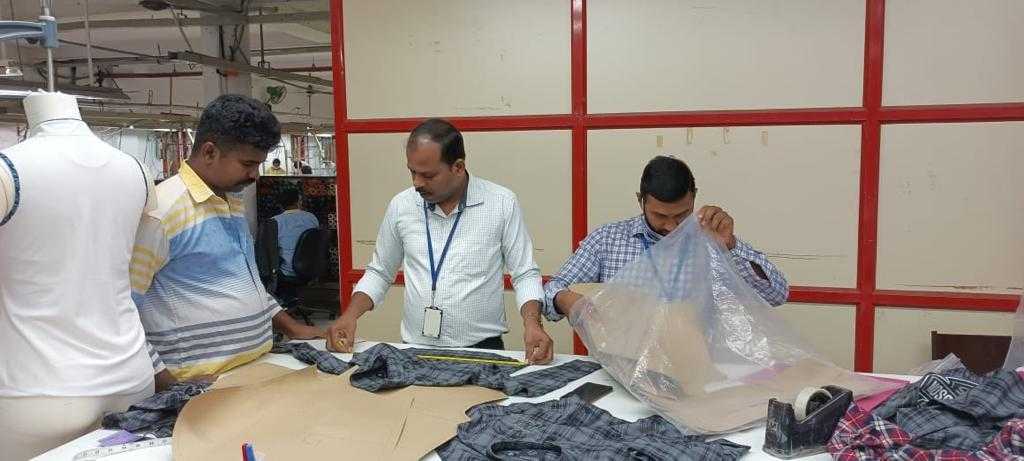
In the garment manufacturing industry, we have to constantly update ourselves and update our capabilities. The requests from our clients will always have some new aspect which we must learn to create and incorporate into our designing and developing capabilities. Guna master’s approach is in tune with this philosophy, “everyone has a lot to learn including me. I keep updating my skills. When a tailor needs help with a new design I help them and make sure the new skills are transferred to them.
Q. What does the leadership position you hold mean to you and how is your relationship with your team?
“I feel a 100% responsibility to ensure that the work is done well and is done on time. From the time the indent is issued till the sample is approved the entire process is under my supervision. I have to ensure it runs smoothly. If the sample is approved it’s on me and if it’s rejected it’s on me. We have to work together and make it overall successful. With my team, I feel like, you have to maintain a good relationship with your tailors.
It’s very important for both Shekar Sir and I that we don’t differentiate between female and male tailors. We only look at the work they do and their salary is only based on their capability.
By maintaining a good relationship throughout makes communication easy. They will understand the things you explain to them better, when a mistake is made they will acknowledge your correction. It won’t work if you are yelling at people all the time. You have to keep your relationship at a 100%.”
It is also inspirational to us that Guna master’s approach is always that of collaboration. He discusses the issue at hand together with the respective person and finds a solution. For instance, when there is a style with smocking, it’s not feasible to make a CAD pattern accurately and when the mock-up is being made that has to be taken into account.
According to him collaboration is key when it comes to handling complex styles, “When a complicated style comes in we coordinate with the merchandisers, we inform them that this style is complex so they will have to take care of it at the costing front. After that, we give input on how the style can be simplified as much as possible so that the cost is less. These simplifications are implicit they don’t affect the visual impact of the piece. It will still match the tech pack given by the buyer. I also give my recommendation as to which factory will be best suited for a style.”
When Guna master first walked in through the main gate of our HQ campus, there was just one main building and the production floor. The washing unit was also very small and both the factory and the HQ building shared a personal department. Now we have several buildings, including the one which holds our printing department and laboratory, an extended washing department and a much larger overall workforce.
Q. What makes Indian designs, Indian Designs. What makes the your experience here different from those you have had elsewhere?
“Whenever we have a difficulty, a problem or a complaint or even when we want to just make a suggestion, the top management listens to it and acknowledges it. They are genuinely concerned about the employees. Even when someone is leaving the company they want to know why and if there is anything they can do to retain the employee. This I have found unique to ID in my experience.”
Q. What is the best advice you have ever recieved?
“So my grandfather used to tell us this when we were young and this is also what I now tell youngsters in my family. When you are young, you are eager to start earning for yourself which is okay. But you need to think deliberately about the career you want, not aimlessly take whatever job is available. Study first, and build a foundation for your career. You will have time later to earn money and you will also have more options then.”
There is something about an employee’s role that goes beyond what can be penned down in review reports and end-of-year evaluations. Which is why, we love having such conversations and sharing them, to capture something that cannot be quantified. The way someone speaks and communicates with others, the energy they bring in.